You should upgrade or use an alternative browser.
Another 944 Turbo Engine Rebuild Thread
- Thread starter dlknight
- Start date
Today I was feeling a bit better after a couple of co-codamol tablets (but also a little sleepy), and thought I'd have a go at installing the rods and pistons in the block.
First mistake was not having the piston lined up properly in the ring compressor (slightly tilted) so I ended up borking the bottom oil ring and control ring. Luckily no other damage, so I will have to find out if I can order replacement oil rings from Mahle for one piston. After learning my lesson I was able to smoothly install the next piston into the bore.
NOTE: If you need any more than a gentle tap on the piston to push it into the bore then something is wrong, do not continue! (I blame the co-codamol!)
With the second piston successfully installed (in cylinder #4) I checked the rod bearing clearance (3 times), with plastigauge.
This was when I decided to stop as I was seeing quite a tight clearance which was confirmed by the previous measurements I'd made with the micrometer. The table below shows my measurements taken with a micrometer and telescopic bore gauge.

My clearances are within Porsche specification (0.034mm - 0.092mm) but outside of the recommendations from ACL - these give around 0.0020" or 0.0517mm minimum.
ACL Race Series performance engine bearings can be assembled with .00075-.001" per 1" of journal diameter (0.020-0.025mm per 25mm of journal diameter) plus .0005" (0.013mm)
Looks like the rods for cylinders #2 and #4 have slightly smaller BE diameters, I switched the rod bearings from #1 to #4 to see if it changed the clearance but got virtually identical measurement (which appears to be telling me it is the rod).

Spent some time this evening doing some research and I've had a bit of a think about this, and I understand you can mix the extra clearance bearings with the standard clearance bearings according to the ACL information.
It is common practise to adjust oil clearances by mixing bearings of adjacent grades i.e. HX-STD with H-STD or H-STD with H-001 or H-0.025, to obtain desired oil clearance. Using the HX-STD with H-STD will give .0005" (0.013mm) additional clearance than using two H-STD shells, and similarly using H-STD and H-001 will reduce clearance .0005" (0.013mm). This, in effect provides the engine builder with 5 potential clearance grades* of 0.0005" (0.013mm) increments.
https://aclperformance.com.au/faq
Going with the following combinations of H-STD and HX-STD bearing halves gives me the following clearances which are much better.
I've packaged my rods up anyway for the machine shop to double check for me but looks like I will be ordering a set of the HX-STD bearings so I can tune my clearances.

Thanks Stuart, it's great that there are people out there like AMAC to keep our classics going. I'm really enjoying build up the engine myself and learning a lot at the same time. Sometimes you find out about the design choices Porsche made when creating our cars which is interesting in itself. The benefit of getting the shop to do the build is obviously the time saving! It is taking me months to move forward as it has to fit in around work and other hobbiesGreat work but way beyond my pay grade. Glad I sent my block and head to AMAC for all that stuff. £4k including the custom pistons they got made seems a bargain to me but I admire how you are going about this and you will certainly get there and be proud of the result.
Even with setbacks hopefully it will all come together, I know if I don't get my rods checked out that it will just be something I would worry about after the engine is assembled. I wouldn't be surprised if the machine shop checks them and say that they are within spec and don't need any work. In that case I will definitely have to go with the mixed upper and lower rod bearing sets from ACL. I guess some of this attention to detail is only warranted when building high performance / race engines (or what they call blue printing) but I always like to do things right!


I'm hoping I can get a set of those oil rings easily and without breaking the bank... (I've reached out to Mahle Motorsport and the local supplier).
scam75
Well-known member
I do enjoy learning but self doubt can creep in. I was starting to convince myself I had re-assembled my wastegate incorrectly before it turned out to be an MBC issue. Having replaced the diaphragm previously I quickly tore it down and then ran into some issues (needed heat eventually) removing the cap and diaphragm from the valve. Then spent ages cleaning it all up then when putting it back together I couldn't convince myself what way up the diaphragm went! Eventually plumping for the way it came out the packet (if you've seen one, you'd understand why, could easily be fitted inside out)! Of course, when I still had no boost control I was convinced I had done something wrong. I should have known when the diaphragm I was replacing wasn't actually damaged, that the wastegate was probably fine, but probably's are never certainties! I was so happy when the new MBC came up trumps and vindicated me!
Anyway, keep the update coming!


They tidied up really well with a wire brush and a flapper wheel on the outer edge, however when I checked the cleaned-up brake disc with the micrometer they were only just within spec (around 30.6mm). So I ordered a new pair from autodoc for £160 (ATE brand), plan is to paint the bells of the new discs the same as the rears and then I can fit them and the repainted front calipers!
Another job was to reassemble the belt tensioner after vapour blasting and plating of the disassembled parts, came up excellent, was pretty tricky trying to get the large spring back into place as takes a lot of force to compress it!

Cleaned the oil pan and baffle to remove any traces of vapour blasting material and reassembled (with red loctite on the screws).

Sneaked in a couple more jobs, replacing some of the a/c o-rings at the bulkhead and installing the re-plated hood catch.




Popped over to Knight Engine Services and picked up the last bits of the engine including the cylinder head and the rods which had been checked and passed with no issues.

Cylinder head inlets have been flowed, ported and larger valves fitted, my original head was cracked and luckily, I had a spare head with Andrew Sweetenham's name on it, so that was used for the rebuild. You can see the crack on my original head below, between the water jacket and a bolt hole.





Extra clearance rod bearings arrived swiftly thanks to David! thanks very much appreciated and the packet of sweets!

Next day I drove up to Tamworth to meet Zeusy and collect some spare panels which may come in useful at a later time.

Most of the day was spent measuring and working out the rod bearing clearances, see below for the final calculations. My micrometer technique has improved so I'm far more confident about these measurements which were verified by the plastigauge later.
Spent the rest of the day re-assembling the rods and pistons, then began installing them into the block!
Installed piston #4 first on its own and made sure the rotating assembly turned freely, then followed up by installing piston #3 and #2 together, finally following by piston #1 the next morning. Check the clearances using plastigauge with each rod, then assembly lube followed by final torquing verified with the stretch gauge.
Used plenty of engine oil this time on the piston skirts, rings, cylinder bores and ring compressor and the pistons installed easily.







I used my stretch gauge which I'd imported from Summit Racing at great expense, but possibly wasn't required as I was achieving the ARP recommended stretch value at the recommended torque.
Final rod bearing clearances below - after reading the ACL documentation, they suggested that it is a common technique to buy sets of different clearance bearings e.g. H-STD and HX-STD, standard and extra clearance. Using one half of each to achieve the desired bearing clearances, the thicker bearing shell goes on the top and the thinner at the bottom.

I was under the impression that a slightly coarser machined finish on the head mating face, gave a better seal with the head gasket.
How to prepare an engine surface for gasket installation.
"OEM MLS gaskets work well on new, flat, clean castings, since they require a very smooth surface finish, usually 20-30 Ra or less."
That said I trust the guy who assembled my cylinder head as he has many years in the business and has a great reputation.
My rubber seat bumper from a VW van from the 60/70s arrived part number 211 881 895A. Looks very similar to the one I took off the brake booster heat shield, although slightly larger. Haven't fitted it yet but I'm optimistic it will fit!

Now I had all the parts back it was time to lay all the clean aluminium pieces out to compare with when they were disassembled from the car late last year.
BEFORE & AFTER


Then onto the next bit whilst I waited for some genuine seals for the oil intake and outlet tubes. Decided to get stuck in and assemble the compensating shafts (balance shafts). I used the Loctite 638 as specified in the workshop manual, although I have heard of people using the alternative flange sealant that is used for the oil pump and lower crankcase section. This was spread onto the cover sealing surface using a mini roller which gave a nice thin layer. Bearings and journals were lubed with some assembly lube before installing the cover. As per the workshop manual the bearing covers were loosely installed with an oiled o-ring and pushed fully home before tightening the covers following the torque procedure.





I got carried away and installed the oil filter console next using the special tool to align the housing.

Paranoia got the better of me and I had ordered a brand new oil thermostat from Porsche, installed this and torqued the cap with a new sealing ring to 80Nm as per the Porsche 928 workshop manual (yes you read that right, for some reason Porsche omitted the torque figure from the 944 workshop manual but it is luckily included in the 928 WSM).

Parts arrived from Porsche so I was able to continue and attach the oil intake and drain tubes.

Then I spent the rest of the afternoon installing the sump, I used a method I'd read on rennlist. I lightly oiled the gasket first so it was wet but not dripping wet. Then loosely installed the gasket on the crankcase, spreading it out correctly. Installed the sump carefully so as to not damage the inlet or drain tubes. Then began to install the bolts by hand, pulling the gasket as needed with a pick tool. I went round several times until all the bolts were tight by hand. Then torqued to 5Nm (my torque wrench didn't go as low as 4Nm as per the manual), again went around many times following the order in the procedure until all the bolts were tight to 5Nm. Then moved up to 10Nm (discrepancy in the workshop manual as the specs at the beginning say 10Nm for step 2 but the procedure in the correct chapter states 8Nm, I went with 10Nm), again seemed like an age going around multiple times until every bolt was 10Nm and there were no more loose bolts. Gasket looks great with no bulges or sticky out bits, ran a paper towel around the edge several times to soak up any excess oil which had squeezed out.

I'm now ready to measure for the head gasket, I think I'm going to go with a Cometic MLS gasket but just need to work out the correct thickness.
I've measured the wear indicator on the cylinder head at around 23.35mm so slightly below the wear limit in the workshop manual (23.6mm). I've ordered a few parts to make up my own CC'ing kit to measure the combustion chamber capacity. I'm also going to measure the piston level at TDC and measure the piston bowl capacity to give me the figures I need to work out the compression and "squish" factor.
Bits for CC'ing kit -
100ml burette with PTFE tap
Burette stand (not strictly required but wasn't that expensive and makes things easier)
Green food colouring
Isopropyl Alcohol (already owned, for cleaning records, another hobby of mine)
3mm clear perspex cut to size, to seal combustion chamber
Used spark plugs (from this car)
If you made it this far, some tips I found. The victor reinz gasket set doesn't include everything you need to finish the build, and some things like the oil pickup tube gasket are not as good quality as the Porsche ones.
I've ended up ordering the following additional items (specifically for a turbo car) -
1 x O-ring (oil return tube) 99970707940
1 x seal ring (oil pickup tube) 94410713605
1 x Seal (oil level sensor gasket) 94410123302
1 x seal ring (oil sump plug seal) 90012311830 (these are 22 x 27 so should be able to obtain from hardware store)
2 x seal ring A 26 X 32 (turbo oil return pipe) 90012304930 (should be able to obtain from hardware store, I ordered from ebay)
1 x seal ring A 18 X 22 (oil breather pipe) 90012314030
4 x seal ring A 14 X 18 (turbo oil feed pipe) 90012300730
2 x O-ring (turbo o-rings) 90017405840 (these are mega expensive, presumably because they are odd size 25x3.15mm)
2 x seal ring A 22 X 27 (oil cooler seal rings) 90012301130 (should be able to obtain from hardware store, I ordered from ebay)
1 x O-ring (turbo oil feed seal) 99970704340
Splendid work and much shininess! Loving the care and attention to detail. Also glad I stuck my block and head on a pallet and sent to AMAC.............
Will be interesting to compare costs on your build vs mine.
Edited! I remembered wrong, it was cheaper!
blade7
Well-known member
I trust the head fettler with 40+ years success building race heads. OEM gaskets aren't the only game in town.How to prepare an engine surface for gasket installation.
Before you install any Fel-Pro gaskets the surface of the engine must be fully prepped.www.felpro.com
"OEM MLS gaskets work well on new, flat, clean castings, since they require a very smooth surface finish, usually 20-30 Ra or less."
That said I trust the guy who assembled my cylinder head as he has many years in the business and has a great reputation.
Alusil? the Mahle pistons have offset pins as well, Nikasil was an option but would have added another £1.5-2k to the total!Same ball park then albeit different rebuild strategies. Can honestly say I feel no difference with iron liners vs Nikasil. No slap at all from cold but AMAC did offset the rod pins to minimise this.
scam75
Well-known member
Fitted the bearing covers to the compensating shaft housings, unfortunately I messed up with the lower bearing cover! I installed the oil seal without the shaft sleeve / collar, so had to remove the oil seal and wasn't able to do so without damaging it. I needed a few other bits from Porsche so ordered a replacement oil seal and had to wait for that and the other bits before I could continue.
In the meantime I'd received a new pair of ATE front brake discs from Autodoc. I wanted these to match the rears which I'd painted with Halfords silver brake caliper paint (I've also done this to the rear discs on the 996, fronts on the winter to-do list). Note to self don't paint them in the utility room, I ended up with a layer of silver paint on surfaces and objects I'd left in the utility room.



The original alternator / aircon pulley was badly corroded, brand new one from Porsche was around £150, but I spotted a nearly new condition one on ebay for about £60 from Poland. At some point Porsche changed the design of the pulley (possibly for the 968) and so the new version comes with 8 mounting holes. The compensating shaft pulley has also been revised to have the same number of thread holes for mounting the new pulley. I don't see an issue using the new alternator / aircon pulley with the original compensating shaft pulley. My old pulley must have been out of balance as the machine shop took an angle grinder to the edge of it! Looked like all the balance weights had rusted to dust. Don't fret I also have a nearly new power steering pulley to keep up the clean look.
New part numbers -
94410211612 - alternator / aircon pulley
94410220912 - compensating shaft pulley / gear




Another fantastic bargain, I found a NOS genuine Porsche engine mount for £150! (just need to find another now!)

Next job was to fret about head gasket sizes and which one to get, I also needed to measure the engine block and cylinder head to assist with the calculations. I measured the piston deck clearance with my VW dial gauge tool and a cheapish dial gauge. After moving it around several times I was able to get a repeatable measurement on each piston / cylinder of 0.28mm above the deck (which meant the pistons are slightly protruding into the combustion chamber), after reading many forum posts this appears to be quite common (possibly even on blocks that haven't been machined). I also measure the cylinder head at the factory measurement point and got around 23.33-23.35mm (which is slightly below the wear limit in the workshop manual). However after much reading, it seems that the most important measurement is the piston deck clearance. To maintain the same combustion chamber size and "squish" I stuck with the factory piston to head clearance of around 1mm (based on the installed height of a stock head gasket). This is around 0.040", which is on the safe side for piston to head clearance when using steel rods (I believe aluminium rods need more clearance). In fact some engine building guides I read suggested 0.030" was safe for piston to head clearance.



With this in mind I added my piston to head clearance (0.28mm) to 1mm, giving approximately 1.30mmm this translated to a gasket compressed thickness of 0.051". Next problem was to work out which gasket bore size I should be ordering, there is much conflicting advice on this, so I went with the most common sense approach and checked it with the manufacturer of my chosen gasket, Cometic. They confirmed that I should be ordering a gasket at least 0.5mm to 1.5mm (0.020" to 0.060") larger than my cylinder bore (factory gasket has 102mm bores). So finally, after much back and forth and reading late into the evening I ordered a Cometic 0.051" 101.5mm head gasket (3-layer). Now I just have a little wait for it to be manufactured and shipped to the UK.
Cylinder Head Combustion Chamber CC measurement
The skimming of the cylinder head below the wear limit has a small effect on compression, however the scientist in me wanted to play with some lab equipment. So I ordered a 100ml burette from ebay (bargain price of around £15, bought some food colouring from the supermarket, and some clear perspex cut into circles. I already had some isopropyl alcohol, distilled water and some silicon grease. Drilled out one 6mm hole in the perspex circle to let the fluid in and allow air bubbles out. Stuck the perspex to the cylinder head combustion chamber with some silicon grease. Then with some premixed fluid (1/2 IPA, 1/2 distilled water, and a drop of food colouring), filled the burette and then measured each combustion chamber in turn to give me a measurement in CCs. Oh and don't forget to fit some old spark plugs to make sure that it is watertight!




With each cylinder head combustion chamber measured I got the following results.

I fed this into the excellent Mahle Motorsport Compression Ratio Calculator - https://www.us.mahle.com/media/usa/motorsports/cr-calc.xlsx
Along with the head gasket measurements from above gave me the following results - the top row is for planning and allows you to enter a target compression ratio, it will then recommend how much "dish" is required on the pistons. My pistons had already been purchased, and technically could be modified, but as you can see, they only make a small change to the compression ratio (my pistons have a 21cc dish).

So a modified compression ratio of approximately 8.42 : 1 (factory is supposed to be 8.0 : 1).
I was also aware that the difference in height of the camshaft by skimming the block and head can alter the timing. This took a while to figure out and find an explanation that I could use to work out.
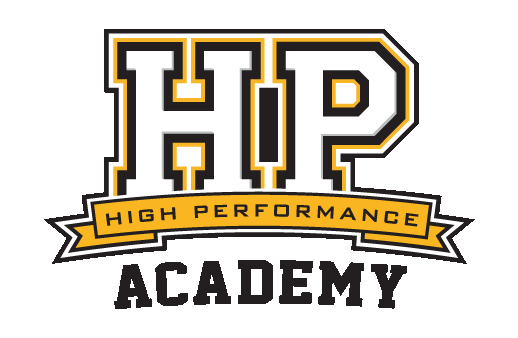
Cam timing and TDC after Head and block milling

Now I know why I should have paid more attention to trigonometry in maths class!
So first you need your camshaft pulley diameter = 120mm
Next how much material has been removed (let's say 0.28mm from the block, and 0.65mm from the head, for a stock head thickness of 24mm) double this measurement as we are bisecting the chord and angle) = 1.86mm (this will be the chord length)
This gives us 1.77625 degrees, we halve this for the camshaft because it is half of the arc, which gives us 0.88812 degrees (retarded).
A very small change to timing which should be perfectly fine.
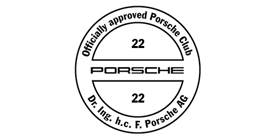
Posts made and opinions expressed are those of the individual forum members
Use of the Forum is subject to the Terms and Conditions
Disclaimer
The opinions expressed on this site are not necessarily those of the Club, who shall have no liability in respect of them or the accuracy of the content. The Club assumes no responsibility for any effects arising from errors or omissions.
Porsche Club Great Britain gives no warranties, guarantees or assurances and makes no representations or recommendations regarding any goods or services advertised on this site. It is the responsibility of visitors to satisfy themselves that goods and/or services supplied by any advertiser are bona fide and in no instance can the Porsche Club Great Britain be held responsible.
When responding to advertisements please ensure that you satisfy yourself of any applicable call charges on numbers not prefixed by usual "landline" STD Codes. Information can be obtained from the operator or the white pages. Before giving out ANY information regarding cars, or any other items for sale, please satisfy yourself that any potential purchaser is bona fide.
Directors of the Board of Porsche Club GB, Club Office Staff, Register Secretaries and Regional Organisers are often requested by Club members to provide information on matters connected with their cars and other matters referred to in the Club Rules. Such information, advice and assistance provided by such persons is given in good faith and is based on the personal experience and knowledge of the individual concerned.
Neither Porsche Club GB, nor any of the aforementioned, shall be under any liability in respect of any such information, advice or assistance given to members. Members are advised to consult qualified specialists for information, advice and assistance on matters connected with their cars at all times.